Mining can be a tough job. It requires long hours, massive machinery, and lots of patience. However, if the conveyor fails and everything else comes into a halt.
It takes both time and time attempting to fix the issue. The reason smart operators are switching to higher-quality conveying equipment is. They’re also more efficient, safe and more cost-effective over the long term.
If you’re using your old system 5 or 10 times ago, it may be the right time to make an upgrade. We’ll look at the reasons why it’s a good idea to consider investing in a more durable, better mining conveyor system.
Lower Downtime, Better Output
The old conveyors fail frequently. The belts slide, the motors break and rollers become jammed. Any breakdown will mean that the entire business ceases to function.
Money is flying out of the window. Modern systems can stop this. They’re designed for extreme circumstances. They last longer with no issues and require fewer repairs in the event of an emergency.
For instance, a mining facility in Queensland, they reduced their downtime by half after switching to a more efficient belt system. This isn’t just less headaches.
This means more ore is moved and loaded onto trucks, plus more money on the final day of the shift. No operator likes delays. Better conveyors give less of them.
Energy Savings Add Up
Conveyors consume power. The more belts you have is, the more you’ll pay. Newer models use power in a more efficient way. They are equipped with powerful motors, adjustable speeds as well as more comfortable operating controls.
A copper mine in Chile decreased its energy consumption by 18% by replacing its belts and drives. This may seem like a small amount at first, but when you look over a period this will add too.
Particularly when prices for power rise. Older systems run at full speed even though they don’t have to. It’s as if you leave your car operating while you’re being parked.
Safer Sites, Happier Teams
Safety isn’t about a checklist that you check, but the difference between a safe shift and serious injuries. Conveyors that are older have exposed components as well as more pinch points and a lot more potential for problems to occur.
Any single conveyor slip could put anyone at risk. Modern systems have better security as well as sensors and automatic shutoffs. They spot problems before they occur and shut down before anybody suffers injury.
Maintenance crews do not require a crawl into narrow places as frequently. Less exposure, less risk. Gold mines located in South Africa saw fewer injuries after they upgraded the conveyor systems.
Tougher Gear For Harsh Work
Mining doesn’t happen in gentle places. Heat, cold, dust, water–you name it, your gear faces it. Mining and resources conveying that are older begins to wear out quickly when operating in these conditions.
The latest models are made to last. More durable belts seal bearings, sealed bearings, and corrosion-resistant frames. This means less rust and less snagged belts and no unexpected shutdowns in the rainy season.
Consider the iron ore mining site located situated in Western Australia. The new belts lasted more than two years before their first major repairs. It’s not just a lucky break.
Smarter Tracking And Control
There’s no way to repair what isn’t tracked. The older systems provide only a few details, maybe a speed reading or a warning indicator.
The latest models provide everything including tension of the belt, temperature of motor as well as load weight along with wear levels. Certain models even let you know when there’s a problem.
The data can help to plan your maintenance rather than being patiently waiting for the things to break. One facility situated in British Columbia saved thousands just through switching to a monitor drive system.
Wrap-Up
If you’re operating at a mine, then you recognize that the margins can be tight. In the event of delays, they can hurt. In addition, breakdowns can be painful.
However, the solution doesn’t need to be difficult. Improved conveying systems can save you time, reduce costs, and protect your employees.
It’s all done without having to constantly watch your children. Imagine this: your conveyor is running every hour than the mine you work in.
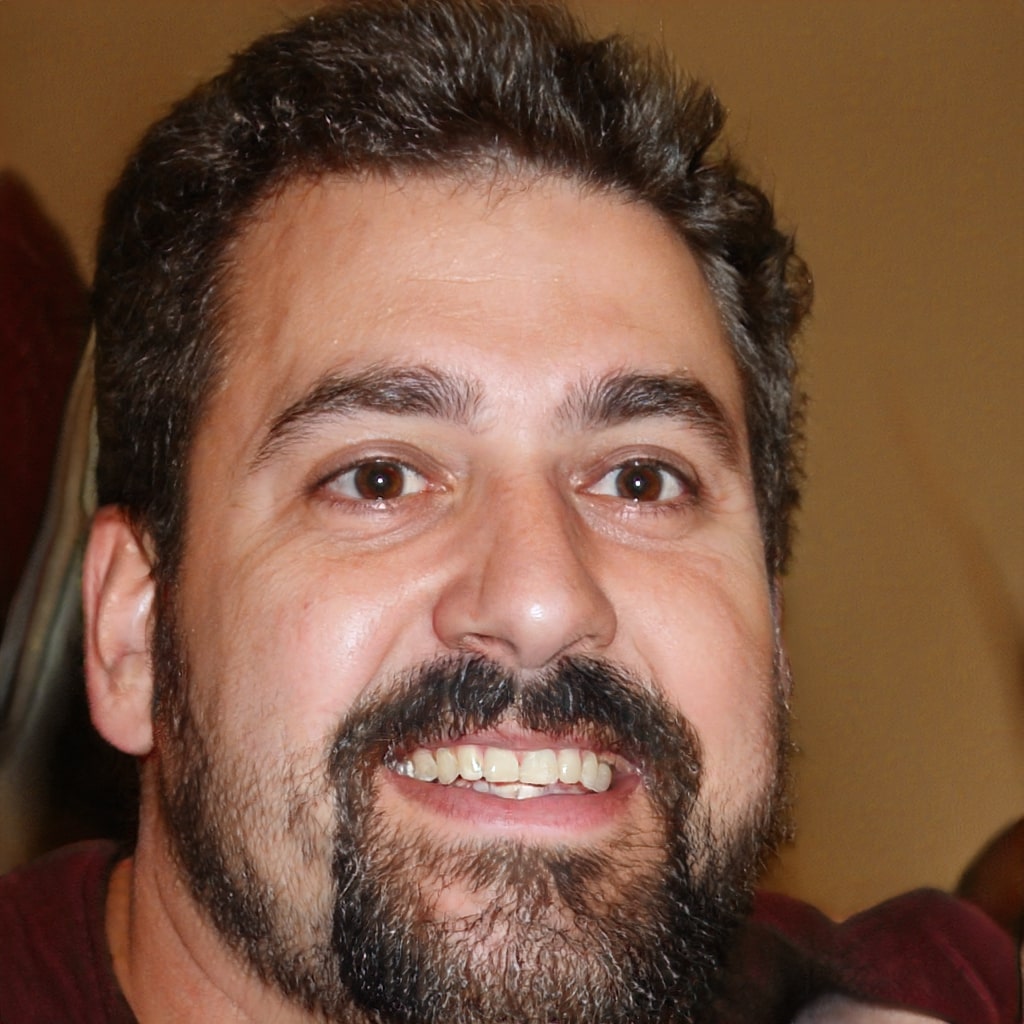